About Us
INDUSTRY LEADER
PrintArt has been
creating connections since 1981
At PrintArt we are committed to helping our customers get their merchandise to market easily, quickly and economically. Since we began creating connections for our customers in 1981, we have been a forward-thinking client-driven company. Throughout our history we have continued to invest in manufacturing space, technologies and equipment to better serve our customers.
COMMITTED WORKFORCE
PrintArt has been in business for nearly 40 years, and our success can be directly attributed to our skilled and dedicated workforce. We have many employees with more than 30 years of experience, and 60% of our staff has 15 or more years of service with the company.
AGILE
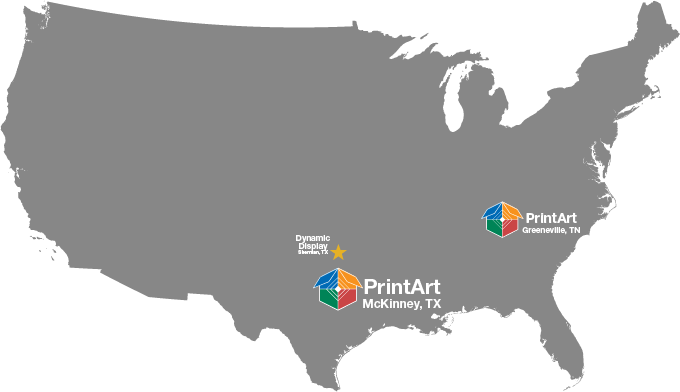
Where we are
With locations in the Midwest and Eastern United States, PrintArt can save you both time and money on your shipments into and out of our facilities.
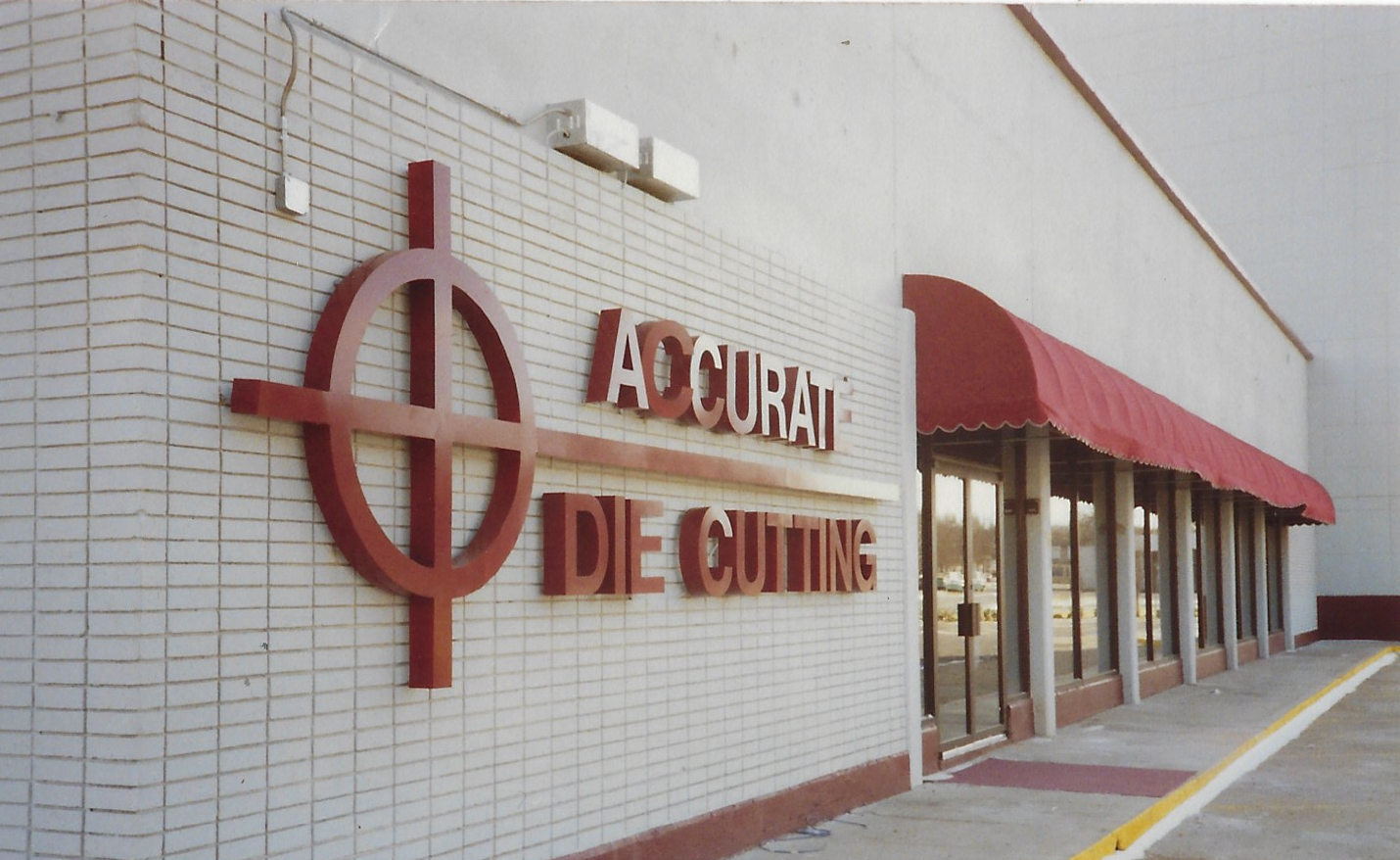
Where we have been
Who would have thought that what began as a way for Bill Alguire to make an additional car payment would evolve into one of the premier graphics facilities in the Southwest? Throughout our history, we have been a customer-driven company that will continue to let our clients determine how we can best serve their merchandising needs.
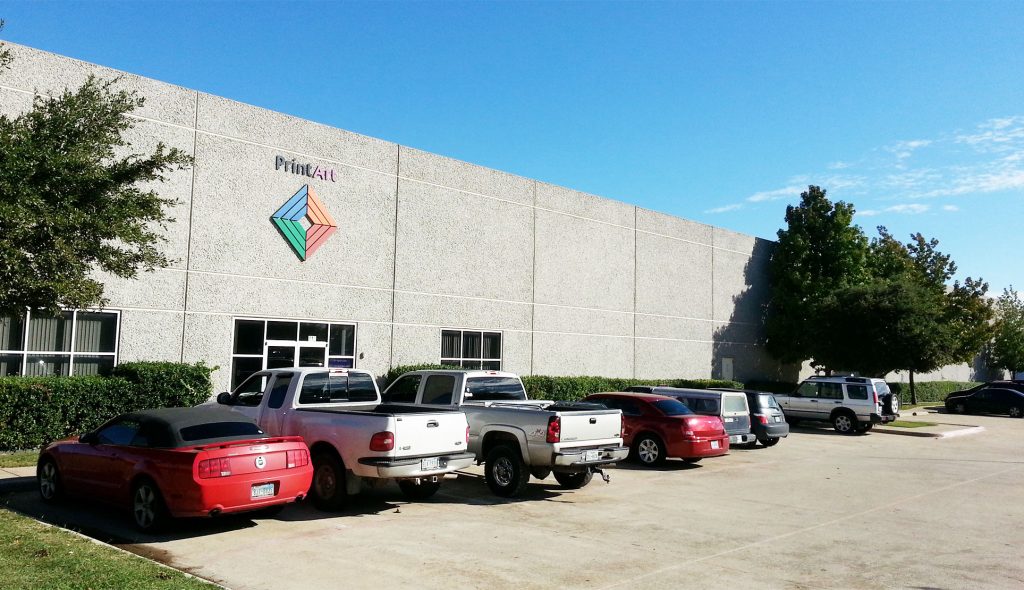
Where we are going
Print Art continues to grow and add capabilities as our partners’ needs evolve. We are excited about our future and look forword to working with you.
EMPLOYEE SPOTLIGHT
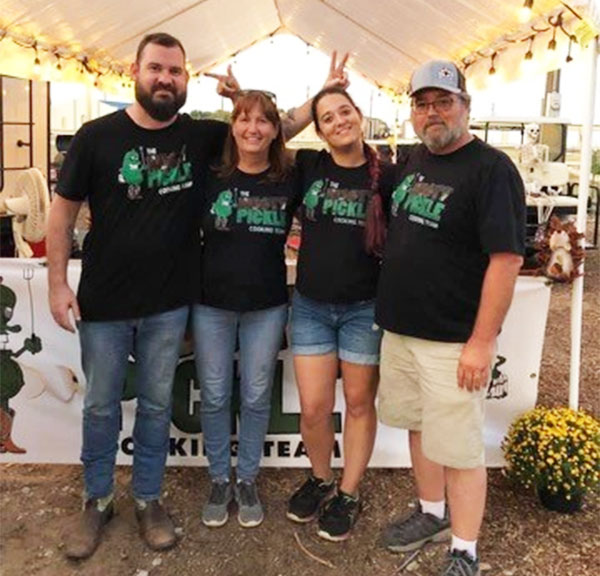
Get to Know Us:
This month we would like to introduce Rusty Locke.
For an unemployed, 24-year-old, high school graduate with chickenpox, 1987 was not shaping up too well. Luckily I’ve always been mechanically inclined and when an opportunity to do some handyman work came along, I was happy to take it. Besides duplexes that needed a little TLC, the KAL investment company that I was working for also owned a 10,000 sf manufacturing facility and they were in need of some help on the production floor. July 27, 1987, that’s when I became a part of the Accurate Die Cutting family. I started as a helper on a die cutter, worked up to an operator, helped with maintenance, and then taught myself to make cutting dies. I went so far as to have 50 promo ink pens made with Rusty Locke / Die Maker foil stamped into them. A couple of years go by and I work myself into a scheduling, supervisory role.
The business was growing, and changing, so in 1990 we bought a 25,000sf, old SAFEWAY grocery store and renovated it. We filled it with equipment and went to work. As word got around about our capabilities and our reputation grew, we expanded again by starting another facility in Dallas and added offset printing and UV coating to our list of services. In an effort to help identify ourselves, we added dba/PrintArt to our name.
By the end of the 90’s we knew we wanted to get everyone together under one roof so we built a 65,000sf building. We set a brand new printing press there and finished the building around it. We were finally all back together, for maybe a month or so in 1999. Workload dictated that we must move some equipment back to the 25,000sf building so we did, and added additional woodworking equipment to support the ever-changing market.
Through prudent and diligent moves by owners and upper management, we’ve continued to grow and expand into additional markets. In conjunction with our efforts in Texas, we’ve nurtured and grown very similar manufacturing processes in Greeneville, TN that have almost doubled our square footage and capacities. We’ve come a long way and I’m very proud to have been part of it.
As Plant Manager of our McKinney operations, I’m very fortunate to work with key personnel. I am able to travel between our locations and know that these folks will not stumble in my absence. Sometimes I have to question if I’m still needed.
At the end of the day, I’m still the same simple guy that I was back in the beginning. I’m an avid music lover that will pull into the driveway and just sit in the truck waiting for a song to end. I hate commercials so I stream all of my music. I do not believe that the digital world is fair to musicians and that’s why I always try to go the extra mile(s) to support live music.
Through the years I’ve befriended many Texas artists, but Baton Rouge holds the road trip record thus far. That’s also why I buy so much merch. I really will never wear (all of) the 100’s of t-shirts I own; not to mention the hats. However, another shirt or CD sale may get the band one more mile down the road. And, nothing goes better with music than a ribeye or some good Texas BBQ. I enjoy cooking them both, but like eating them more. You do get a great deal of satisfaction from preparing a meal for family and friends and having them tell you how much they enjoyed it. Even when you know it wasn’t your best.
At Print Art, our people make the difference.
PrintArt has been in business for almost 40 years and we continue to grow day by day. We have recent machine additions to keep up with the growing demands of our clients.
- 1981: Accurate Die Cutting in a 400 Sq. Ft. mini warehouse.
- 1984: Moves into a 10,000 Sq. Ft. manufacturing facility in McKinney, Texas.
- 1989: Purchases a 20,000 Sq. Ft. manufacturing facility in McKinney, Texas.
- 1993: Opens Dallas Facility.
- 1995: Installed our first printing press. A Komori 6-color press as well as changed the company's name to PrintArt.
- 1999: Upgraded our in-house printing capability by adding a Mitsubishi 6-color press as well as building and opening a new 65,000 square foot manufacturing facility in McKinney, Texas.
- 2005: Opened a new 65,000 square foot manufacturing facility in Greeneville, TN. and launched our Extranet Order and Inventory Management System.
- 2010: Opened a Moulding and Millwork facility in upstate NewYork.
- 2012: Purchased and installed a Fujifilm Acuity Flatbed Digital Inkjet Printer.
- 2015: Purchased and installed a Xerox J-75 Digital Printing Press.
- 2018: Purchased and installed a Komori G-40 LED 6 Color Printing Press.